Yarrow's Spiderweb
At the farmhouse kitchen sink, looking out a window at the front yard, I saw suspended, hanging in air, a long, thin twig and slender leaf. Slight, intermittent breezes moved the dangling tree debris about, made it obvious against the gray sky. It hung about head-height above the lawn, bobbed up and down and around a few inches.
I guessed the twig was attached to a very thin thread of spider or caterpillar silk. But with no tree branches at least 30, likely 40 feet above the twig, this was a very long thread. The length and strength of this nearly invisible, whisker-thin strand of spiral protein impressed me. To stretch so far, to remain whole, tugged by breezes, tiny coiled-coil protein fibers, with amazing strength and flexibility.
Next day, out the kitchen window, I saw the twig was still bobbing slightly at head-height. This strength and persistence further impressed me.
Feet planted, I started to take photos. Suddenly, the twig flew at me — swung directly at me, forced me to bend back. I almost fell, stumbled sideways, tried to set my feet, snap another photo. I had to wait for the twig to stop swinging, and hold position long enough to snap the shutter.
I managed to click the shutter twice, when a new breeze blew the twig at me again — this time more vigorously, and I had to step backward. The twig blew higher, for longer time while I tried snapping photos of an erratic moving object.
Eventually, wind relaxed, twig returned to hang over the bare patch, I tapped the shutter button again. In the vigorous wind, I thought the thread had stretched and lengthened. But surprise — its height hardly changed! Evermore impressed by the tenacious strength of almost-invisible spiral biostructure.
Suddenly, a third time, the twig twirled toward me. Forced to evade it, I stopped snapping photos. Three times wind blew this bobbling body straight at me, forcing me to hobble and stumble around to get my photos.
Astonished the almost invisible thread didn’t break, I assumed the force of the wind had stretched the slender strand of silk, lengthened its coiled proteins, by inches, even a foot. I expected the twig to swing back closer to the ground. But the wind passed, the twig sank, slightly low at first, then slowly rose back head-high, as if the thread stretched, then recoiled and tightened.
Is a spiritual intelligence embedded in this land? Is this ghostly trick or treat by a twig a Halloween gift from a poltergeist? A mystery message from an Earth Spirit? My respect deepened for spiders and caterpillars. Amazing a single strand of spider thread kept twig and leaf suspended head-high in two cool, moist, unsettled days.
— David Yarrow, November 2017 (edited with permission)
Spider silk arrives at the end of an unbroken 400 million year strand of continuous evolution. Some silks are for structural support, others protective enclosures. Some absorb energy, others transmit vibration.
Each spider and each type of silk, produced from different glands and spin techniques, has a set of mechanical properties optimized for its function. A dragline silk, the kind observed by David Yarrow, is produced in the Large Ampullate gland and has tensile strength greater than high-grade steel alloy. Draglines are for the web’s outer rim and spokes and also the lifeline by which spiders dangle.
Spiders make webs that can span rivers but the strands are so thin and light they could circle the earth and still weigh less than 500 grams (18 oz.). If while transecting the Earth the strand crossed the poles or the Sahara it would not weaken. Dragline silks can hold their strength below −40 °C (−40 °F) and up to 220 °C (428 °F) — more than twice the boiling point of water.
Silks are extremely ductile — able to stretch 5 times their relaxed length without breaking. They are adhesive — created by a two-compound pyriform secretion from the Flagelliform gland. They are spun into patterns that polymerise under ambient conditions, become functional immediately, and are usable indefinitely. They are waterproof but biodegradable, versatile and fungal resistant while remaining compatible with most other materials in the environment. At the end of their life, many webs are simply consumed again by the spider to reclaim the embodied metabolic energy.
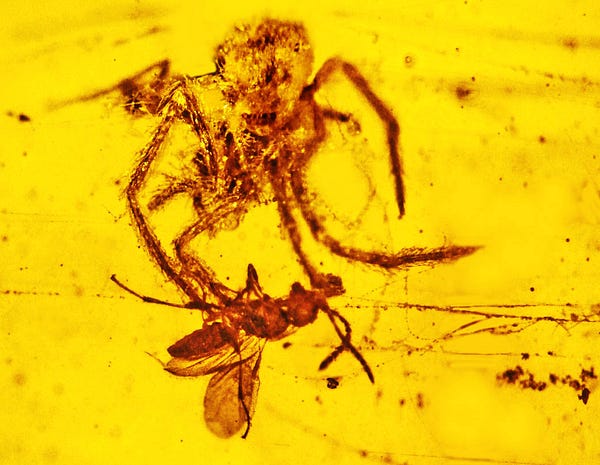
A spider web preserved in amber, thought to be 110 million years old, shows evidence of a perfect “orb” web, the most famous, circular kind one thinks of when imagining spider webs. An examination of the drift of those genes thought to be used to produce the web-spinning behavior suggests that orb spinning was in an advanced state as long as 136 million years ago. — Wikipedia
Some wandering spiders will leave a largely continuous trail of silk impregnated with pheromones that the opposite sex can follow to find a mate. They may also produce sperm webs or egg webs. Some webs are impregnated with venom. Some water-borne spiders build a diving bell of silk. Some canopy spiders balloon or kite on airborne weaves.
All these miraculous feats are made possible by carbon. The silken strands are woven from amino acids, primarily glycine (C2H5NO2 ) and alanine (C3H7NO2). Credit must go to the spider for the way in which these are arranged. Silk production is a pultrusion, similar to extrusion, with the subtlety being that the force is induced by pulling from the glands rather than being squeezed out. As a thread is pulled away from the body of a spider, whether by the spider’s legs or by the spider falling under its own weight, shear stress and ion and pH changes induce the liquid silk to undergo a phase transition and condense into a solid protein fiber with specialized molecular organization. Depending on the gland that crafted the protein and controlled movements within the spinnerets, the silk can be for dragline, adhesion lines, temporary scaffolding, attachment points, the web frame, egg sacs, capture spiral, or prey cocoon.
Silks are often referred to as a block co-polymer. The short side chained alanine is mainly found in the crystalline domains — giving strength. Glycine is mostly found in the elastic semi-amorphous regions with their helical and beta turn structures. These two carbon chains interplay to give spider silk some of its extraordinary properties, but the carbon rings in pyrrolidine (CH2)4NH keep the silk moist and gluey while also warding off ants. Other enzymes protect the lines from fungi and bacteria that might otherwise digest the proteins.
New applications are being discovered for its mechanical, conducting, electrical, biocompatibility and immunologic properties. Spider silk has been experimentally used in garment weaves, electrical sensor and actuating devices, suture threads, biomimetic muscles, nerve regeneration, and ligament tissue repair.
Nicola Maria Pugno at the University of Trento and a team of researchers in Italy and the UK found a way to incorporate carbon nanotubes and graphene into spider silk and increase its strength and toughness beyond anything that has been possible before. The resulting material has properties such as fracture strength and toughness higher than anything ever measured.
Pugno’s team collected 15 Pholcidae spiders from the Italian countryside, sprayed the spiders with water containing carbon nanotubes or flakes and then measured the mechanical properties of the silk the spiders produced.
Giving spiders water that is infused with carbon made them weave silk stronger than any known fiber. Could this lead to a new class of bionic materials? As yet, no one has been able to make this work commercially, but not for lack of trying. Kraig Biocraft Laboratories (Trading Symbol: KBLB) is focused on commercialization of genetically engineered spider silk.
The problem with commercializing spider silk has always been the ornery attitude of spiders. As the Italian researchers described it:
Unlike the case of the largely available silkworm silks, large-scale spider farming and synthetic production of spider silk still remain to be achieved, due to its complex structure and the territorial and cannibalistic nature of spiders. Moreover, naturally spun fibres, obtained by forcible spinning, harvesting or extracting spidroin from glands, have reduced mechanical characteristics with respect to naturally-spun ones, due to the CO2 anaesthesia of spiders and the consequent loss of active control of their silk spinning. Research to improve the mechanical, conductive or magnetic properties of spider silk has been limited. This is due to the difficulty of developing an adequate spinning methodology, balancing extrusion, drawing, yield and purity. … Attempts to improve or modify the mechanical, magnetic and electrical properties of spider silk have been reported, using techniques such as melt-spinning, templating, powder coating, atomic layer deposition and iodine doping, but they remain to be adequately perfected, especially at large scale, using naturally spun spider silk fibres.
The graphine doping test was proof of just how hard spider farming can be.
The best mechanical performances are observed for the samples after the first collection. The second collection does not show mechanical enhancement with respect to the first or to RS [control], probably due to a physiological spider weakening during segregation, since neither additional food nor water were available during the experimental period, except SWNTs and graphene dispersions. In the cases marked with an asterisk in Figs. 5b,c, the second collection was impossible since the corresponding spiders died. Note that spider 5 died after the first treated dragline silk collection, but was able to spin the silk with the maximum increment in mechanical performance, whereas spider 7 spun the silk with the highest absolute values and survived.
Kraig Labs was originally interested in competing with the Chinese raw silk market worth $3–5 billion per year. After inserting genes from the golden orb weaving spider into silkworm strains, the lab produced 20 separate caterpillar clones, each with unique properties, able to spin silk with the strength, flexibility and resiliency of spider silk. Now Kraig is looking at the much larger, $120 billion technical textiles market. A 3rd generation modified silkworm is expected to spin fibers exceeding the strength of spiders’ and may incorporate gene sequences that release an antibiotic and to develop sutures and bandages that help patients to heal faster and to reduce scarring.
For those concerned about the risks of genetically engineered spiderpillars being scaled into the trillions, the company’s choice of a trademark will not be reassuring — Monster Silk®.
This story, though, is not about genetic engineering. The story is about carbon. Life depends on carbon. What we term “organic chemistry” is shorthand for carbon chains and the molecular structure of living things. For a variety of reasons, life cannot arise from silicon or any similar element with covalent bonding. If can only come from carbon, formed only under the special conditions of the death of a star.
After a radiant life lasting billions of years, a star runs out of hydrogen. It begins to cool, change color, and expand into a red giant. At its core, helium is compressed until the forces are strong enough to begin fusing nuclei (proton-neutron pairs or “alpha particles”) to form larger atoms such as carbon. The red giant begins to collapse until the central temperature rises to 108 million °Kelvin, seven times hotter than the core of our Sun. This creates a situation called triple-alpha, by which nucleosynthesis of heavier elements begins. The power released by the birth of carbon is approximately proportional to the star’s core temperature taken to the 40th power and the density squared. As such extreme temperature spikes it causes the reaction rate of fusion to spike. This positive feedback cycle becomes a runaway until the fuel is exhausted.
This process — a “helium flash” — lasts only seconds but burns 60–80 percent of the helium in the star’s core. During the flash, the star’s energy production can reach approximately 100 billion solar luminosities, comparable to the luminosity of a whole galaxy. Compared to a birth of helium, the birth of carbon is as royalty.
Arriving on the solar wind some 4 billion years ago, carbon stardust lingered for a time in Earth’s atmosphere before hitching a ride on a raindrop and falling into the ancient oceans. There it bonded with hydrogen to form some of the earliest chain molecules we call “organic.” As these molecules formed nucleoproteins and began to reproduce themselves, the oceans came alive with a carbon food web. Carbon became a common denominator of all known life that followed.
Arachnids emerged at least 380 million years ago from crab-like chelicerate ancestors. They were among the first to leave the sea and move out onto land; the oldest known land arthropods. Indeed, they helped form the land by building the first soils.
We are, like spiders, carbon creations that have learned to use carbon as tools. We harvest it for food, we burn it for fuel, and lately, we have even relearned the lost skill of building soil with it.
We inhabit an era when the natural carbon cycle has been disrupted. We can take credit for that. Now we are compelled to learn to put it back the way it was. We won’t do that by breaking the rules. We just might if we can learn from David Yarrow, and spiders, and remember that carbon is our friend.
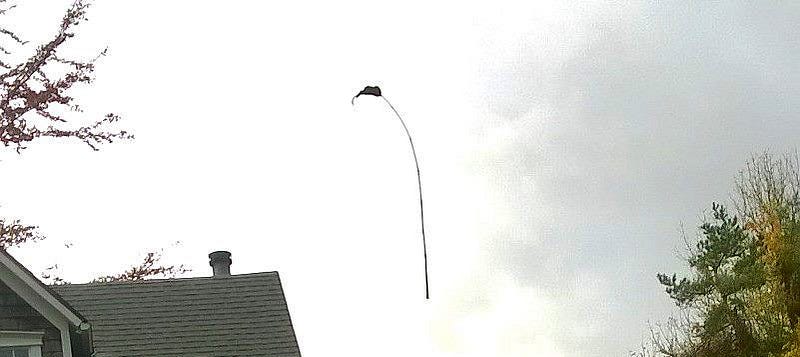
Comments